18 months of implementation = successfully completed project
Project implementation started: ICT solutions for more competitive products
ESCO-Fofonjka ltd. is 05.02.2020 based on the successful passage of the call Improving the Competitiveness and Efficiency of SMEs through Information and Communication Technologies (ICT) - 2 concluded an agreement with the Ministry of Economy, Entrepreneurship and Crafts and the Croatian Agency for Small Business, Innovation and Investment on project co-financing (grants).
Project title: ICT solutions for more competitive products.
Main project activities:
- Procurement of ICT business solutions intended for the improvement of business processes
- Implementation, adaptation and integration of business solutions with the existing / new ICT system
Goals and expected results: The main goal of this project is to increase competitiveness by investing in ICT solutions by increasing the efficiency of warehousing, construction departments, accounting and procurement processes, and thus contribute to the realization of strategic goals of the Industrial Strategy and regional / local goals and development documents. With the realization of the project, the company expects to increase the number of employees, increase sales revenue, improve 4 business processes and use the grant.
Total project value: 1,154,246.05 KN (including VAT)
Amount co-financed by the EU: 637,143.81 KN (excluding VAT)
Project implementation period: from 15.01.2020. to 15.07.2021.
News:
08/20/2020. – during 6 months of project implementation, we realized all 10 activities planned in this 6 month period. In addition to project visibility activities (publications in digital and print media, poster and labels), we purchased computers with all components and operating system for storage and control, server memory, innovative 3D modeling program SolidWorks Premium 2020 and document management program SolidWorks PDM Professional CAD Editor 2020.
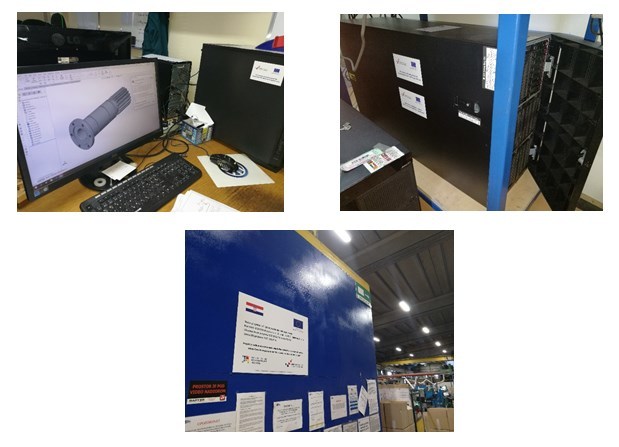
11/22/2020. – after 9 months of project implementation, we have realized 11 activities out of a total of 16 planned activities. In the third quarter, we acquired and implemented SolidWorks Professional 2020, a 3D modeling program that includes a database of standard mechanical parts and assemblies. This activity also included a program of testing and training employees in the process of upgrading the 3D modeling program, and ultimately provided us with quality construction and design of products, tools and machines.
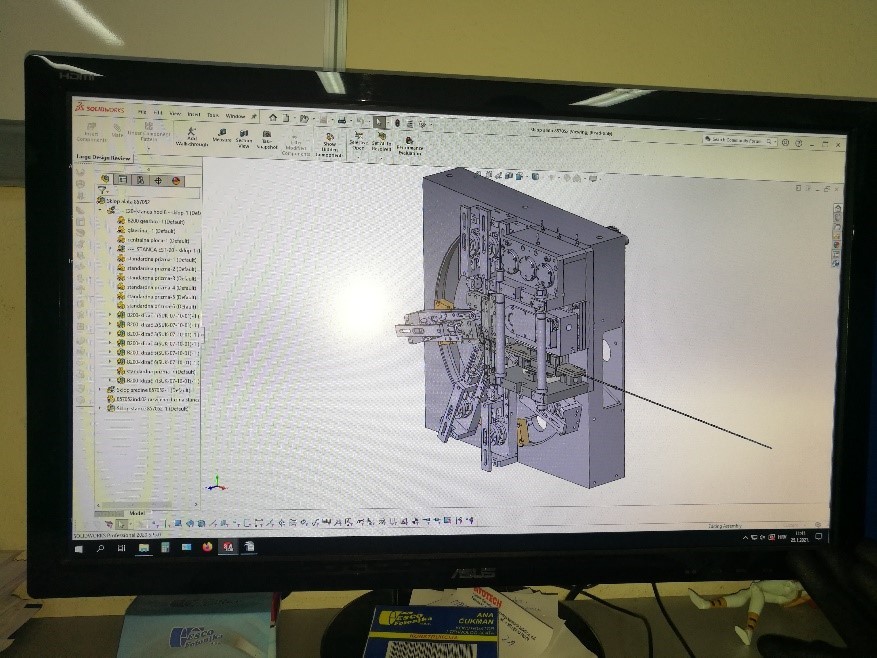
02/22/2021. – after 12 months of project implementation, we have realized 13 activities out of a total of 16 planned activities. In the fourth quarter, we acquired and implemented the WMS information subsystem with a bar code that uses smart devices and bar code readers to automate the receipt, storage, manipulation, reservation and shipment of warehousing items, inventory, traceability of production processes and analysis of activities and reporting.
We also procured and implemented for the warehouse a program for the production of labels for marking products, raw materials, consumables, tools and spare parts and tool steels. By implementing this program, the company has enabled the digital transformation of the entire labeling process, from design to label printing. The consequence of the implementation is more fluid and agile operations that enable the company to respond more quickly to changes in market conditions and customer demands.
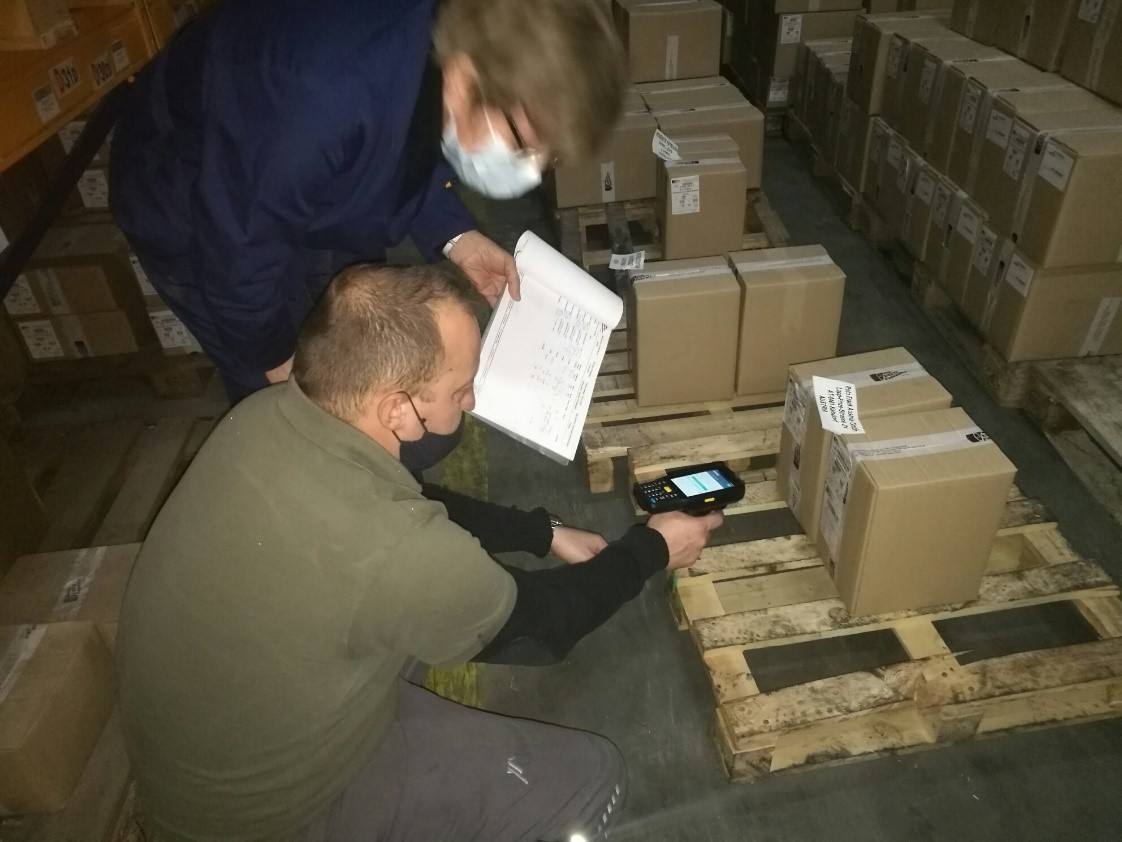
05/31/2021. – after 15 months of project implementation, we have realized all 16 activities out of the total planned. In the fifth quarter, we acquired and implemented SolidWorks Plastics Professional 2020, a SolidCAM milling software package with associated modules and FikusWorks wired postprocessors.
SolidWorks Plastics Professional 2020 is a program for the development and technological preparation of the production of plastic products based on 3D models, version 2020. The program is installed on existing computers in construction department, as well as a specialized program for the construction of tools for plastic products.
- The mentioned program enables credible simulation of key parameters during the construction and design of the mold and the product itself, and over time reduces the development costs of plastic products.
- The program is intended for the development and technological preparation of the production of plastic products based on 3D models, with injection molding technology.
It serves to simulate the process and speeds up the process of constructing injection molding tools and reduces the number of required attempts and thus reduces the cost of manufacturing injection molding tools.
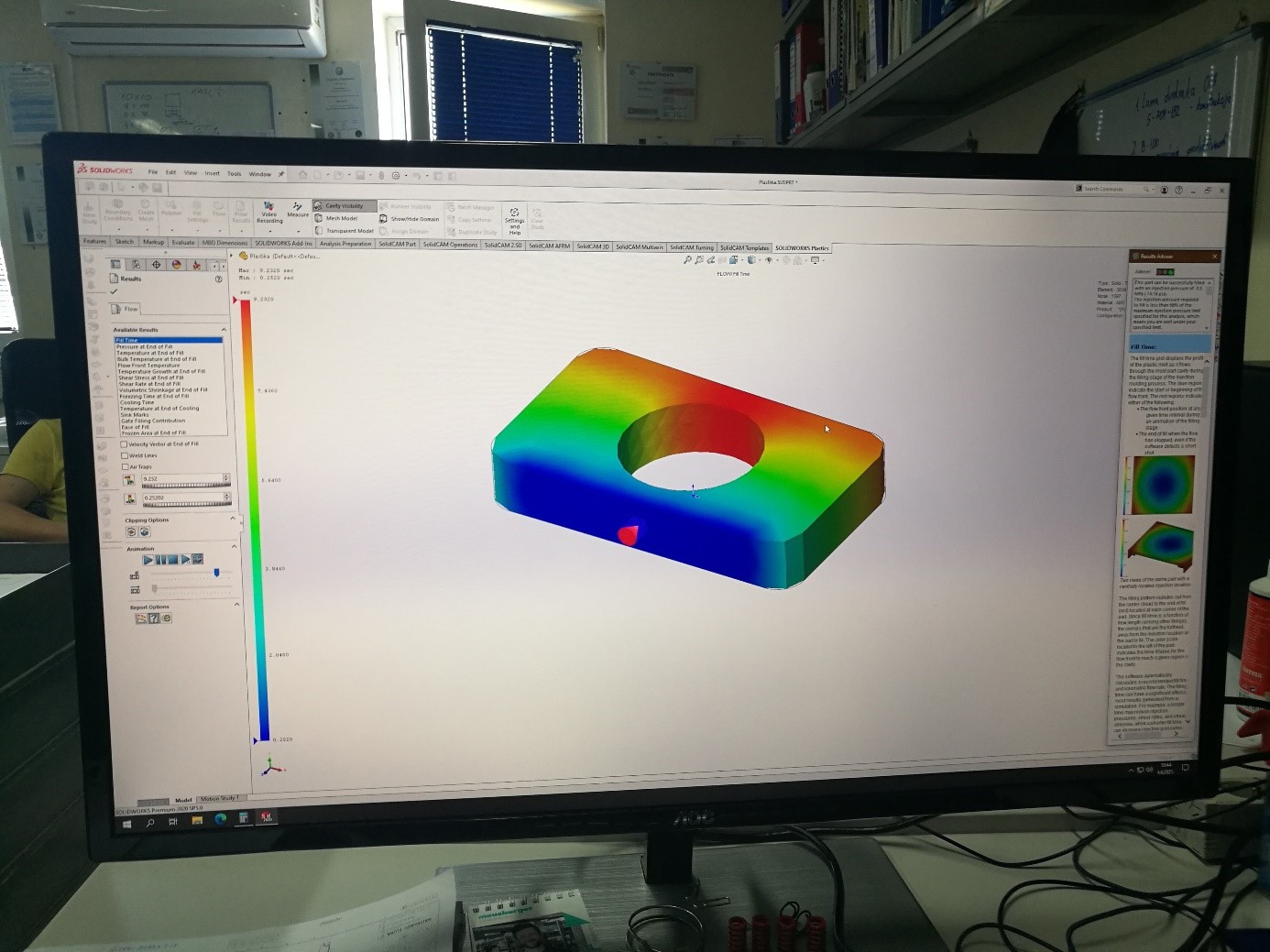
The SolidCAM milling software package with associated modules includes:
- SolidCAM milling 2.5 D or equivalent - (2 pcs),
- HSM module for high-speed processing or equivalent - (2 pcs),
- HSS high-speed surface milling or equivalent - (2 pcs),
- 3D I - Maschining CNC machining or equivalent - (2 pcs),
- Program for automatic hole detection - (2 pcs) and
- Postprocesor SolidCAM 4x ili jednakovrijedno- (1 kom)
The current mode of operation includes manual model processing and CNC program development for program machining centers. Using the previously mentioned package of programs would speed up the processes of making demanding parts of tools, as well as making molds for plastic injection, and products and machines. The software package speeds up faster preparation of milling technology and reduces errors since the program is generated directly on the model.
A program that quickly generates program code for creation on CNC machines based on 3D models. It contributes to speed and reliability, as there is no rewriting but the code is generated from 3D models.
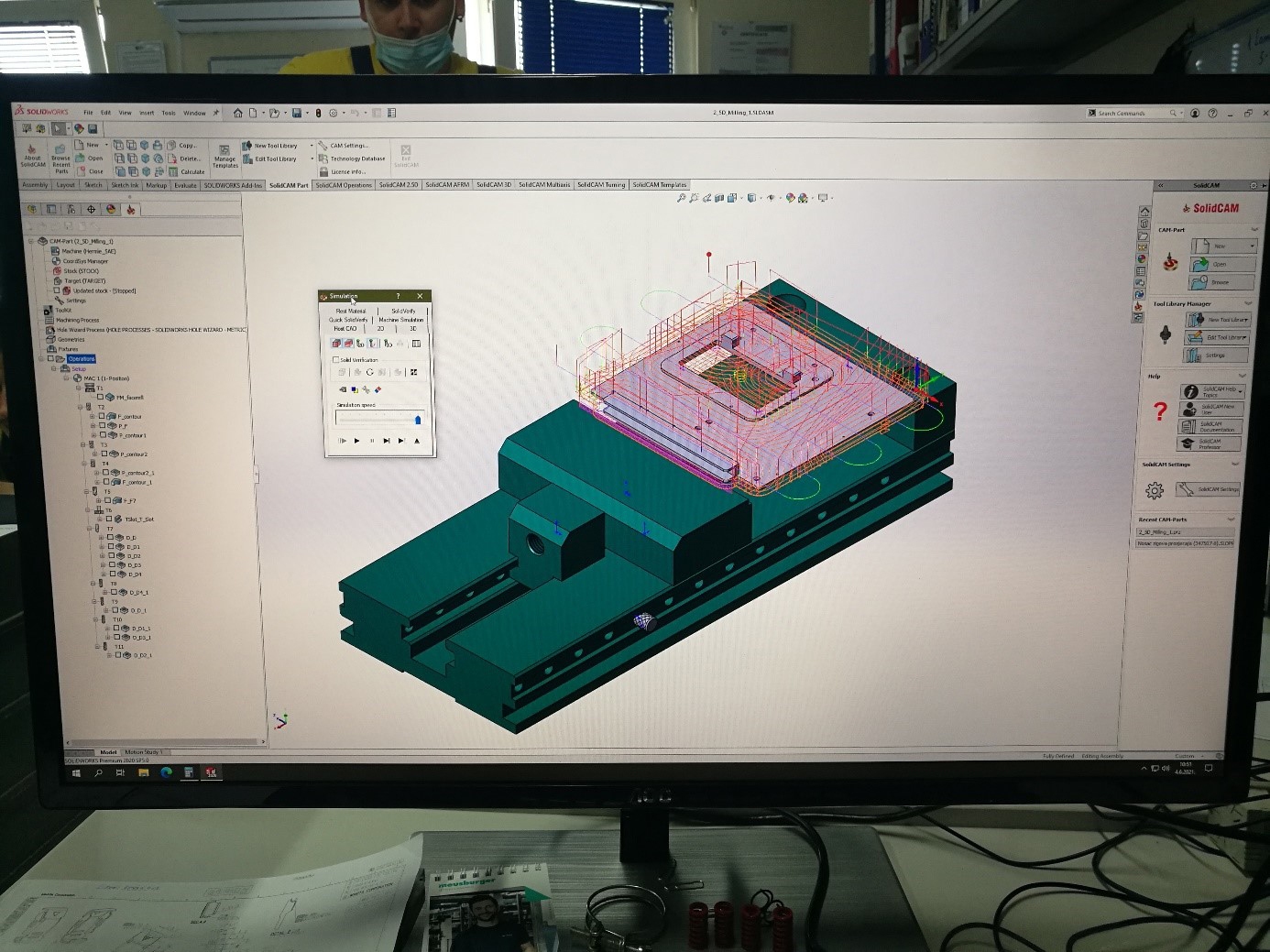
FikusWorks wire with postprocessors speeds up the processing of drawings and the creation of the program for erosimat - a machine that works on the principle of electroerosion.
- Postprocessor is a part that is implemented in a computer tool for designing engineering products (CAD or equivalent), in order to better adapt the CNC program to a specific type of CNC machine.
- Accelerates the process of creating a CNC program and reduces the possibility of error.
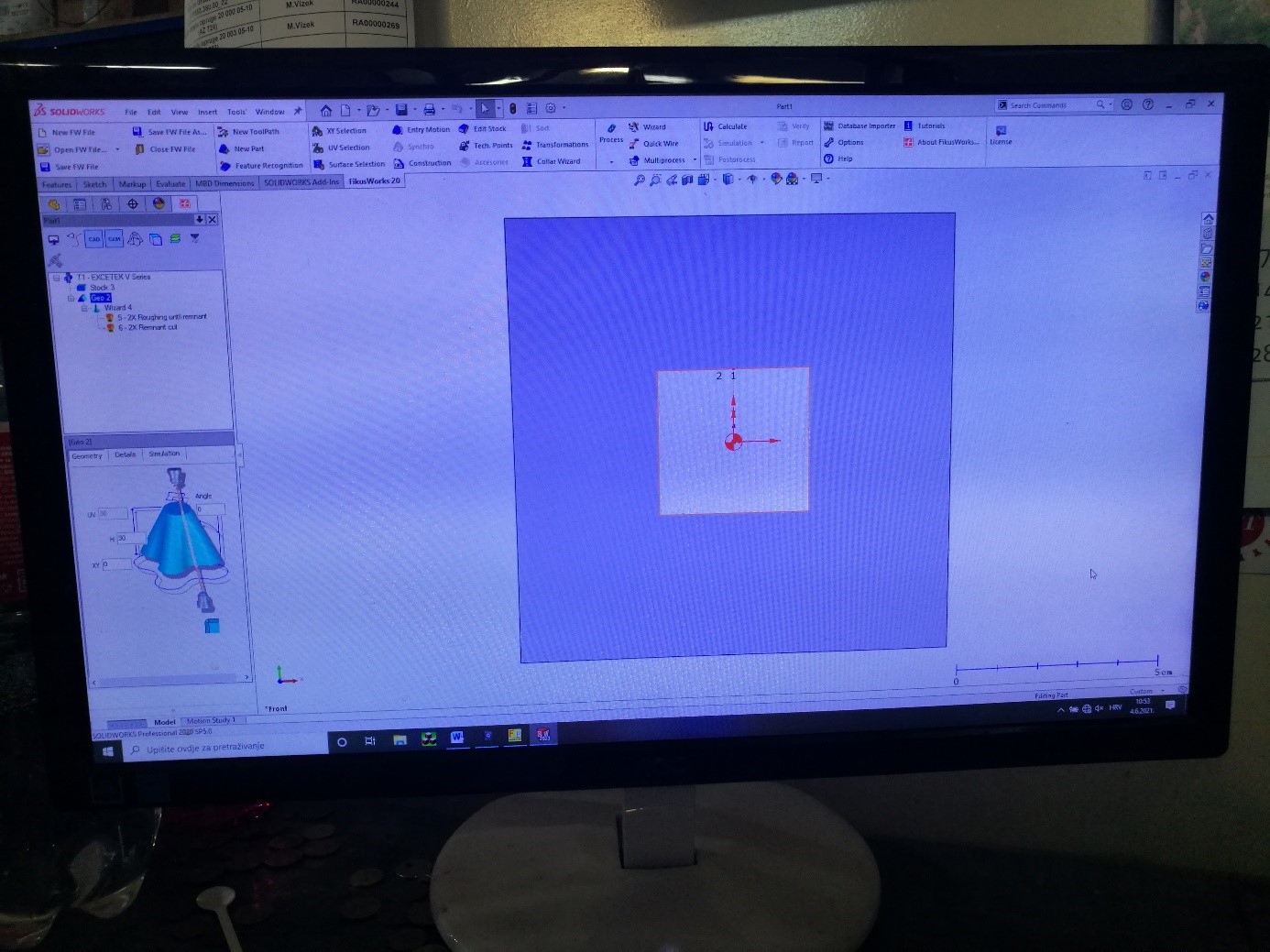
07/20/2021 - after 18 months from the signing of the contract and the beginning of realization, on 15.07.2021. we have successfully completed the project.
Despite the crisis caused by the covid-19 virus pandemic and all its negative consequences for the economy (extended delivery times, etc.), we successfully implemented all the activities envisaged by the project in a timely manner. The advance obtained at the beginning of the implementation enabled us to finance the project stably over the next 18 months, and out of HRK 965,874.78 of realized costs, we received HRK 618.516,29 in grants through 6 submitted requests for reimbursement. Procured software and equipment are in operation and progress is already visible in the processes of construction, warehouse management, accounting and procurement. There is also an evident increase in the number of employees and total sales revenue.
![]() European Union |
![]() Together to EU funds |
The project was co-financed by the European Union from the European Regional Development fund.
Contact person for more informations: Nenad Mrzlečki
Links to relevant sites: www.strukturnifondovi.hr
